In The News
- 2025
- June
- May
- April
- March
- February
- January
- 2024
- December
- October
- September
- August
- June
- May
- April
- March
- February
- January
- 2023
- November
- October
- September
- August
- July
- June
- May
- April
- March
- February
- January
- 2022
- December
- November
- October
- September
- August
- July
- June
- May
- April
- March
- February
- January
- 2021
- December
- November
- October
- September
- August
- July
- June
- May
- April
- March
- February
- January
- 2020
- December
- November
- October
- September
- August
- July
- June
- March
- February
- January
- 2019
- December
- November
- October
- September
- August
- July
- June
- May
- April
- March
- February
- January
- 2018
- November
- October
- September
- August
- July
- June
- May
- March
- February
- 2017
- December
- November
- October
- September
- August
- July
- June
- May
- April
- March
- February
- January
- 2016
- December
- November
- October
- September
- August
- July
- June
- May
- April
- March
- February
- January
- 2015
- December
- November
- October
- September
- August
- July
- June
- May
- April
- March
- February
- January
- 2014
- December
- November
- October
- September
- August
- July
- June
- May
- April
- March
- February
- January
- 2013
- December
- November
- October
- September
- August
- July
- June
- May
- April
- March
- February
- January
- 2012
- December
- November
- October
- September
- August
- July
- June
- May
- April
- March
- February
- January
- 2011
- December
- November
- October
- September
- 2017 Best Places to Live in America (1)
- 2024 West Chester Economic Development Report (1)
- 2025 Mustang Club of America National Show (1)
- 3 new tax districts to promote West Chester development (1)
- Aaron Wiegand (1)
- Advanced Manufacturing (1)
- Advanced Technology Consulting (1)
- AdvancePierre (1)
- AdvancePierre Foods (1)
- AdvancePierre Johnsville Sausage West Chester Ohio (1)
- AdvancePierre largest private company in region (1)
- AdvancePierre names new CEO (1)
- Advantage RN West Chester Ohio (1)
- AK Steel (6)
- AK Steel Corporate Headquarters West Chester Ohio (1)
- AK Steel West Chester Ohio (1)
- Al-Joe's (1)
- Aloft (1)
- Aloft Hotel (1)
- AMC Theatre (1)
- Amylin Pharmaceutical BioTech BioOhio Manufacturing West Chester Ohio (1)
- Amylin Pharmaceutical BioTech BioPharm West Chester Ohio (1)
- Amylin Pharmaceuticals FDA Approval West Chester Ohio (1)
- Anest Iwata (1)
- Ashland Valvoline West Chester Ohio (1)
- ASIC (1)
- AstraZeneca (1)
- ATC (1)
- Atmos360 (1)
- AtriCure (1)
- Atricure (1)
- AtriCure Announces Definitive Agreement to Acquire Estech (1)
- AtriCure device shows promise in treating Atrial fibrillation (1)
- AtriCure expands distribution in Japan (1)
- AtriCure FDA Approval (1)
- AtriCure Receives FDA Approval for Investigational Study (1)
- Atricure West Chester Ohio (1)
- AtriCure West Chester Ohio (2)
- Available Retail Sites (1)
- Aveda Fredric's Institute West Chester Ohio (1)
- Awards and Rankings (1)
- BAE Systems West Chester Ohio (1)
- Barnes Aerospace (1)
- Bass Pro buys land for new West Chester store (1)
- Bass Pro Outdoor World (1)
- Bass Pro Shop (1)
- Bass Pro Shops (4)
- Bass Pro Shops moving to West Chester (1)
- Bass Pro Shops Outdoor World (1)
- Beckett Commons (1)
- Beckett Springs (1)
- Beckett Springs Hospital West Chester (1)
- Beckett Springs Hospital: Mental health facility set to open in West Chester (1)
- Beckett Springs Mental Health Hospital (1)
- Beckmark (1)
- Becknell building (1)
- Beef Jerky Outlet (1)
- Beer 30 (1)
- Bel Haven (1)
- Bella Vino Wine Merchants & Bar (1)
- BEST COMMUNITY TO DO BUSINESS (1)
- Best Place to Live (1)
- Best Places to Live (2)
- Best Places to Live 2016 (1)
- BGR (1)
- biopharmaceutical (1)
- Blue Ocean Robotics (1)
- Boys & Girls Club of West Chester (1)
- Boys & Girls Club of West Chester and Liberty (1)
- Boys & Girls Club of West Chester/Liberty (1)
- Boys and Girls Club (1)
- Breakout Games (1)
- Bridge Logistics (1)
- Bristol-Myers Amylin Pharmaceuticals West Chester Ohio (1)
- Bristol-Myers Squibb (2)
- Buffalo Wings and Rings (1)
- BUSINESSES KEY TO WEST CHESTER’S SUCCESS (1)
- Butler County adds year (1)
- Butler County Clerk of Courts (1)
- Butler County Finance Authority (1)
- Butler County manufacturers growing (1)
- Butler County RTA (1)
- Butler Tech (4)
- Butler Tech Bio-Science Campus (1)
- Butler Tech Bioscience Campus (6)
- Butler Tech BioScience campus coming to West Chester (1)
- Butler Tech Bioscience Campus expansion (1)
- Butler Tech Bioscience Center (3)
- Butler Tech Bioscience Education Facility (2)
- Butler Tech BioScience Education Facility (1)
- Butler Tech moves forward with bioscience facility (1)
- BUTLER TECH: COMMITTED TO AN EDUCATION REVOLUTION (1)
- Cabela's (4)
- Cabelas (6)
- Carepoint Nursing (1)
- Casa Bianca (2)
- Cascades at Union Centre (1)
- Centre Park Holiday Inn Event & Banquet Center (1)
- Centre Park of West Chester (2)
- Centre Park of West Chester to bring Holiday Inn & Suites (1)
- CFM International (8)
- Chick-fil-A (1)
- Children’s Learning Adventure (1)
- Christian Brothers Automotive (2)
- Chuy's at The Streets of West Chester (1)
- Chuys Tex-Mex (1)
- Cincinnati Axe Throwing (1)
- Cincinnati Curling Club (1)
- Cincinnati lands Super Bowl of site selection conferences (1)
- Cincinnati State (1)
- Cincinnati State Supply Chain Career Development Center (1)
- Cincinnati State’s new Supply Chain Career Development Center (1)
- Cincinnati USA economic development activity (1)
- CincyLink (1)
- Civic Centre Boulevard Extension (1)
- ClarkDietrich Building Systems (1)
- Clubhouse Sports Grille (1)
- CNN Money Best Places to Live 2012 West Chester Township Ohio (3)
- COMMUNITY DEVELOPMENT LAYS FOUNDATION FOR MODERN GROWTH & STABILITY (1)
- Community Entertainment Districts (2)
- Community Foundation of West Chester/Liberty (1)
- Contech buys stormwater filtration company (1)
- Contech Engineered Solutions (1)
- Contech Engineered Solutions LLC (2)
- Contech West Chester Ohio (1)
- Contingent acquires Tampa subsidiary (1)
- Contingent Network Services (5)
- Corghi USA (1)
- COSTAR (1)
- CR Brands (1)
- CSI Pharmacy (1)
- CTL Aerospace (1)
- CTL Aerospace & Kingsgate Transportation (1)
- Custom Millcraft (1)
- Cut Ups Salon (1)
- CyberOhio (1)
- Dayton (1)
- Dayton-based Mexican restaurant expanding into West Chester (1)
- Dayton-based pizza (1)
- DEE SIGN (1)
- Delicious Designs Cookies (1)
- Display Works West Chester Township (1)
- DogBerry Brewery (1)
- DogBerry Brewing (3)
- Domino's (1)
- DRT Medical (1)
- DRT Medical - Morris (1)
- Duke Realty spec building on Provident Drive (1)
- Duluth Trading Co. (1)
- E Technologies Group creates 27 new full-time jobs (1)
- E-Tech (1)
- E-Technologies Group adds N.C. office (1)
- Einstein Bros. Bagels (1)
- EnterTRAINment Junction (1)
- Escape the Room Challenge (1)
- Escape The Room Challenge (1)
- Escort (1)
- Esther Price Candies (2)
- Esther Price opens third location in West Chester (1)
- event space (1)
- Exit 19 (1)
- eyes growth (1)
- F45 Fitness Center (1)
- Fameccanica (1)
- Faxon Firearms (1)
- Fifth & Pacific Companies retains jobs (1)
- First Financial Bank West Chester Ohio (1)
- Fit Body Boot Camp (1)
- Fit Food Stop (1)
- Foreign Investment (1)
- Fortune 500 companies West Chester Ohio (1)
- Four Points by Sheraton (1)
- Freddy's (1)
- Freddy’s Frozen Custard & Steakburgers (2)
- Fresh Market West Chester Ohio (1)
- Fricker's (1)
- Frickers (1)
- Frutarom (2)
- GE Additive (1)
- GE ADDITIVE (1)
- GE Additive Center (3D Printing) (1)
- GE Aerospace (1)
- GE Aviation (17)
- GE AVIATION (1)
- GE Aviation 3-D Additive Development Center (1)
- GE Aviation Additive Technology Center (1)
- GE Aviation engine sets record in latest test (1)
- GE Aviation joint venture launches first-of-its-kind program (1)
- GE Aviation joint venture nets $500M deal (1)
- GE Aviation manufacturing technology (1)
- GE Aviation North Pointe at Union Centre (1)
- GE Aviation North Pointe Office Park (1)
- GE Aviation North Pointe Office Park West Chester Ohio (1)
- GE Aviation plans more investments in Ohio on technology (1)
- GE Aviation West Chester (1)
- GE Aviation West Chester Ohio (1)
- GE Aviation/CFM International (2)
- General Electric (1)
- Georgia Pacific (1)
- Georgia-Pacific Corrugated (2)
- GM Family Days (1)
- GOERING CENTER (1)
- Grainworks Brewing Company (3)
- Group Health (1)
- Group Health Tri-Health Physician Partners (1)
- Group Health TriHealth (1)
- Gynecologic Oncology Clinic and Infusion Center (1)
- Hills Properties (2)
- Holtman's Donut Shop (1)
- Homearama 2016 (1)
- hotel rooms to Butler County (1)
- Hotels Union Centre Boulevard (1)
- Hyatt House (2)
- Hydrotech (1)
- I-75 Growth Corridor (1)
- IceTech America West Chester Ohio (1)
- IKEA (3)
- IKEA West Chester (3)
- iMFLUX plans new manufacturing project; Systecon expands (1)
- Inc. (5)
- Inc. (ATC) (1)
- Inc. West Chester Ohio (1)
- Industrial Tube & Steel Corp (1)
- iNET Interactive (1)
- INFRASTRUCTURE (1)
- Infrastructure Improvements (1)
- Intelligrated (1)
- INVESTMENT (1)
- Jack in the Box (1)
- Jack In The Box (1)
- Jack In The Box West Chester Ohio (2)
- Jeannette’s Delicacies (1)
- job growth (1)
- Johnny’s Italian Steakhouse of West Chester (1)
- Katy Kanelopolous (1)
- Kemba Credit Union (2)
- KEMBA Credit Union (3)
- Kingsgate Transportation (1)
- KINGSGATE TRANSPORTATION SERVICES (1)
- Kleingers Group (1)
- Kosei North America (1)
- Kroger Marketplace (4)
- Kubicki Office Park (1)
- LAKOTA CYBER ACADEMY (1)
- LaRosa's (1)
- Liquor Licenses (1)
- Lithko Contracting (1)
- Liz Claiborne remains open (1)
- LOCAL FOOD MANUFACTURER ANNOUNCES PLANS FOR WEST CHESTER EXPANSION, INVESTMENT (1)
- LOFT (1)
- Loft apartments (1)
- Loft Streets of West Chester Ohio (1)
- Logicalis (1)
- Long Stanton Manufacturing (1)
- Long-Stanton (1)
- Long-Stanton Group West Chester Ohio (1)
- Long-Stanton West Chester Ohio (1)
- Main Event (3)
- Main Event Entertainment (1)
- Mak’s Family Pharmacy (1)
- Marriott (1)
- Matt the Miller’s (1)
- Mayfield Brain & Spine (1)
- Mayfield Clinic West Chester Ohio (1)
- Meijer (1)
- Mellow Mushroom (2)
- Mellow Mushroom West Chester Ohio (1)
- Menchie's (1)
- Menchies West Chester Ohio (1)
- Mercedes-Benz of West Chester (1)
- MetroParks Athletic Complex at VOA Park (1)
- MetroParks VOA Athletic Complex (1)
- Miami Learning Center Marks First Decade (1)
- Miami University Regionals (1)
- Miami University Voice of America Learning Center (3)
- MIDLAND ATLANTIC (1)
- Midwest Filtration (1)
- Milanos (1)
- Milanos eyes West Chester location (1)
- Mitt Romney West Chester Ohio (1)
- Mixed Martial Arts Ultimate Fighting Championship (1)
- Moeller Music (1)
- MVG (1)
- NASA taps GE Aviation for new project (1)
- National Resilience (1)
- National Triathlon West Chester Ohio (1)
- Navis Pack & Ship (1)
- Netrada North America (1)
- New Hilton to bring jobs (1)
- NEW KROGER MARKETPLACE OPENS JANUARY 31 (1)
- New Residential Communities West Chester Ohio (1)
- North Ridge Realty Group (1)
- NorthPoint Development (2)
- O'Gara-Hess & Eisenhardt Armoring Company LLC retained jobs (1)
- Oats Overnight (1)
- Octal (1)
- Office space occupancy rate improves in West Chester (1)
- Ohio (3)
- Ohio Butler County ground zero of job growth between Cincinnati (1)
- Ohio Eagle Distributing (1)
- OHIO REPEATS AS RUNNER-UP IN 2018 GOVERNOR’S CUP (1)
- Ohio Wins 2011 Governor's Cub Award Site Selection Magazine (1)
- Olde West Chester new businesses (1)
- Omni Systems (1)
- Orion International (1)
- Outback Steakhouse (1)
- P&G could save $1B a year with new Butler County plant (1)
- P&G plastics unit promises 221 West Chester jobs (1)
- P&G reveals dollar details about 'breakthrough in packaging' (1)
- P&G subsidiary gets zoning approval for West Chester plant (1)
- Panera Bread (2)
- Paper Products Company (1)
- Paris Air Show (1)
- Patty Burger (1)
- Peak 10 (2)
- Permira Intelligrated West Chester Ohio (1)
- Pharmaceuticals Biotech West Chester Ohio (1)
- Pilot Chemical (1)
- Pink Peacock Boutique (1)
- PIVOTek West Chester Ohio (1)
- Planes Moving & Storage (1)
- Planterra Foods (1)
- POLE ZERO (1)
- Pole/Zero (1)
- Port Union at Union Centre (1)
- Port Union Commerce Park (1)
- Premier Shooting & Training Center (1)
- Procter & Gamble (1)
- Raising Canes Chicken Fingers (1)
- Raising Cane’s (2)
- Relax Wash + Fold (1)
- Republic Bank (1)
- Republic Wire (5)
- Republic Wire expansion West Chester Township (1)
- Republic Wire West Chester Ohio (1)
- research (1)
- Residences at Clocktower (1)
- Resilience (3)
- RightSource Humana (1)
- Ripple Junction (1)
- Rite Track Equipment Services (1)
- Rite Track West Chester Ohio (1)
- Salvation Army (1)
- SanMar (1)
- Savoy at the Streets of West Chester (1)
- Schumacher Dugan Construction & Millikin Fitton Law Firm (1)
- SentriLock (1)
- SentriLock to open West Chester global HQ Friday (1)
- Shellback Semiconductor Technology (1)
- Shoot Extreme (1)
- Shoot Extreme West Chester Ohio (1)
- SimplexGrinnell West Chester Ohio (1)
- Skally' (1)
- Skally's Old World Bakery (1)
- Skally’s Old World Bakery (1)
- Small Business Grants (1)
- Snecma (1)
- Sozo Hair at Bajon Salon and Spa (1)
- Spark Grant (1)
- SPARK Grant (1)
- Springstone (1)
- Springstone Beckett Springs Hospital (1)
- Star Manufacturing (1)
- STRATEGIC INCENTIVES DRIVE LONG TERM GROWTH IN WEST CHESTER (1)
- Streets of West Chester (1)
- sub restaurant coming to West Chester (1)
- Sugar Creek Packaging (1)
- Sugar Creek Packing (2)
- Sugar Creek Packing Co. (1)
- SUGARCREEK (1)
- Sunesis Construction (1)
- Sunesis Construction Co. (1)
- Sunesis Construction Company West Chester Ohio (1)
- Surge of new dining options open in West Chester (1)
- SwimOutlet.com (1)
- SwimOutlet.com holds hiring event at West Chester facility (1)
- Swimoutlet.com Spiraledge (1)
- Swing 365 (1)
- Swing365 (1)
- Synchrony Financial (1)
- Systecon (1)
- Taziki’s Mediterranean Café (1)
- The Boys & Girls Club of West Chester/Liberty (1)
- The Comfort Inn & Suites (1)
- The Fresh Market (2)
- The Fresh Market West Chester (1)
- The Learning Kitchen (1)
- The Noble (1)
- The Pickle Lodge (2)
- The Residences at Clocktower (1)
- The Silver Diva (1)
- The Spicy Olive (1)
- The Square @ Union Centre (1)
- The Square at Union Centre (1)
- The Streets of West Chester (6)
- Tikka Grill (1)
- Tom + Chee (1)
- Tom+Chee (1)
- TopGolf (6)
- TopGolf West Chester (2)
- Total Quality Logistics (1)
- Totes Isotoner (1)
- totes-Isotoner (1)
- TradeGlobal (2)
- TradeLane Properties (2)
- Trew (1)
- Trew Automation (1)
- Tri-County Spine and Rehab (1)
- Tri-Health (1)
- TriHealth (1)
- TRIHEALTH (1)
- TriHealth doctors plan expansion in West Chester (1)
- TriHealth medical center (1)
- TriHealth site plan (1)
- TRUSTEES SUPPORT RETENTION OF TWO BUSINESSES (1)
- TSS Technologies (2)
- Tylersville Road widening (1)
- U.S. 42 Revitalization (1)
- U.S. Bank Centre building (1)
- UC Health (4)
- UC Health Orthopaedics and Sports Medicine (1)
- UC Health plans 2nd hospital tower in West Chester (1)
- UC Health West Chester Hospital (4)
- UC Health West Chester Hospital Fieldhouse (1)
- UC Health West Chester Medical Campus (1)
- UC Health, West Chester Hospital (1)
- UC Women's Health Center (1)
- UCB Transportation Improvement Award (1)
- UCBMA Food Truck Rally (1)
- UNION CENTRE 2019 TRANSFORMATION (1)
- Union Centre Boulevard at I-75 (1)
- Union Centre Commerce Park (1)
- Union Centre Office Park (1)
- Union Centre Office Park II (1)
- United Dairy Farmers (1)
- UPS Supply Chain Solutions (2)
- USA Weightlifting National Championships (1)
- Usui International (1)
- VFW Headquarters (1)
- Village North (3)
- Voice of America Museum West Chester Ohio (1)
- Voice of America Shopping Center (1)
- Voices of America Country Music Fest (1)
- Walkenhorst's (1)
- Welling and Co. Jewelers (1)
- West Chester (2)
- West Chester Academy (2)
- West Chester Antique Center (2)
- West Chester Billiards Centre (1)
- WEST CHESTER BUSINESS COMMUNITY THRIVES (1)
- West Chester Butler County Ohio doing business in China (1)
- West Chester Cares (1)
- West Chester chamber of commerce (1)
- WEST CHESTER COMMUNITY DEVELOPMENT (1)
- West Chester Community Development Director (1)
- West Chester could receive its first YMCA (1)
- West Chester Development Council (2)
- WEST CHESTER EXPERIENCES PERMIT GROWTH SPURT (1)
- West Chester Hospital (23)
- West Chester Hospital fastest growing hospital 160 new jobs (1)
- West Chester Hospital Maternity (1)
- West Chester Hospital Maternity Unit (1)
- WEST CHESTER HOSPITAL RANKED IN TOP 10 OF CINCINNATI HOSPITALS BY U.S. NEWS & WORLD REPORT (1)
- West Chester Hospital robotic surgery West Chester Ohio (1)
- West Chester Hospital West Chester Ohio (1)
- West Chester Hospital/UC Health (1)
- West Chester jobs (1)
- West Chester Liberty Chamber Alliance (3)
- West Chester Ohio Manufacturing Industry (1)
- West Chester Ohio's Governor's Cup Award (1)
- West Chester Pet Resort & Spa (1)
- WEST CHESTER RETAIL CENTER GETS MAJOR FACELIFT (1)
- West Chester SPARK Grants (1)
- West Chester Splash Pad (1)
- West Chester Spray Park (1)
- West Chester top employers (1)
- West Chester Township (2)
- West Chester Township continued growth (1)
- West Chester Trade Center (4)
- WEST CHESTER TRADE CENTER (1)
- West Chester wine shop moves to bigger location (1)
- West Chester Zoning Permits (1)
- West Chester's 'hotel row' is booming (1)
- What's New in West Chester 3Q-2017 (1)
- Whole Foods (3)
- Whole Foods Market (1)
- Winelco (1)
- Workforce Development (1)
- Yummy Bowl (1)
Powerful 3D printing of engine parts part of West Chester Twp. company’s new deal
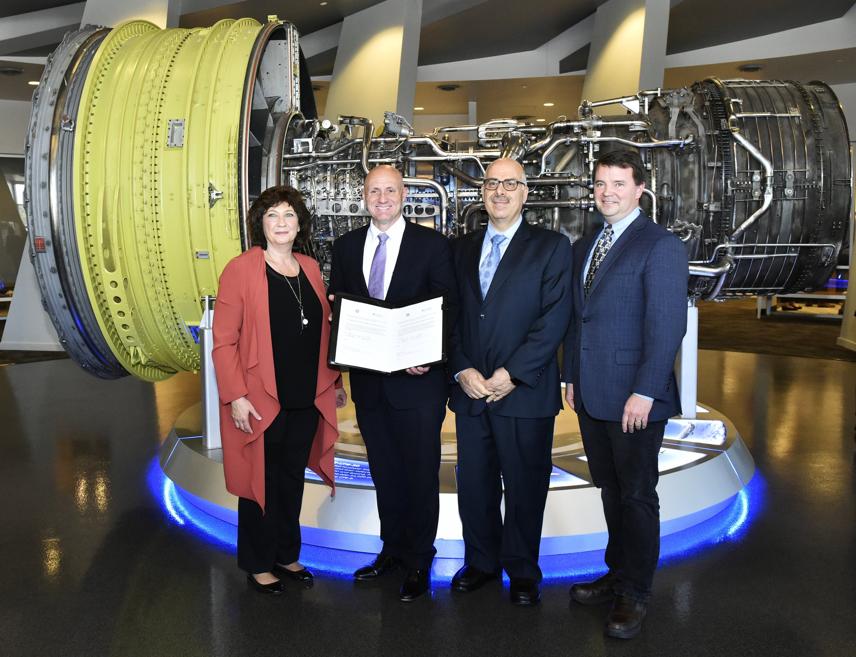
Journal News
West Chester Twp.-based GE Additive needs help designing the 3D printers that create engine parts so advanced that current technology cannot produce them.
That’s why the GE Aviation subsidiary on Monday signed a five-year cooperative research and development agreement (CRADA) partnership agreement with the U.S. Department of Energy’s Oak Ridge National Laboratory, a leader in additive manufacturing.
The two partners will improve energy and material efficiency, utilize domestic energy resources, support production of clean energy and benefit the nation’s economy, ORNL officials said.
The agreement focuses on processes, materials and software to drive broader adoption of additive manufacturing technology.
Daniel Simmons, assistant secretary of the Office of Energy Efficiency and Renewable Energy at the DOE, toured GE’s West Chester facility Monday just before the agreement was signed. He said 3D printed parts have, for a long time, seemed to be “little toys,” when that is not the case.
“These are real parts in the real world. They’re made out of metal, like in some cases you can’t make these parts in another way, and so that’s where it is really exciting,” Simmons said. “It is additive manufacturing made real. This is not toys, it’s real manufacturing.”
GE invested in additive manufacturing, or “3D printing,” more than a decade ago when the technology first came out and Oak Ridge began developing some of the methodology, according Christine Furstoss, GE Additive’s chief technology officer.
“We understood the power of additive to design parts that cannot be produced any other way, to be able to use materials that are very hard to process in any other method,” Furstoss said. “We’ve advanced to really almost outpacing the ability of the process to make the parts. We can design parts that are so intricate, it’s almost hard to image those. We now need machines that keep up with that.”
Since 2015, GE has manufactured 3D printed fuel nozzles for the Airbus A320’s jet engine. The company is working on 60 other designs, using additive manufacturing in some of them to reduce the number of components from 855 to 12.
What’s created by the partnership will “knock down a lot of barriers.”
“We’re really going to bring it to the masses, to small and medium enterprises, to be able to really differentiate themselves and be able to continue to invest in U.S. manufacturing,” Furstoss said.
Additive technology involves putting down a layer of metal powder, then using an energy source to finely write a very intricate shape, she said.
“It’s almost like Etch-A-Sketch, if you remember those days, where you draw it, but we’re doing it layer by layer, and we’re getting properties and shapes no one else could imagine,” Furstoss said. “That takes a lot of technologies to come together.”
Scientists at Oak Ridge, which has Summit, the world’s fastest computer, are using additive manufacturing to design a Transformational Challenge Reactor, a nuclear reactor that’s approximately 3 feet high and about 4 feet in diameter, according to Moe Khaleel, associate laboratory director.
“It’s not about the fastest, it’s about its ability to do things,” Khaleel said. “We can take lots of data, lots of information, and generate very useful algorithms and methodologies to control additive manufacturing such that we can make the right part with the right structure inside the material.”
The agreement supersedes an existing CRADA in place since 2012 between ORNL and GE Additive Arcam EBM.
Furstoss said, “Oak Ridge National Lab understands the process deeper than any other team she knows and has abilities to characterize and test materials in very unique ways.“